In the vast realm of the industrial field, a crane factory is like an iron fortress, writing its own glorious chapter with advanced production equipment and rigorous technological processes.
When raw materials enter the factory like soldiers waiting to be inspected, incoming material inspection becomes the first important checkpoint. Professional inspectors, with keen eyes and a strict attitude, conduct detailed inspections on each batch of materials. No tiny flaw, from the hardness and strength of the materials to the dimensional accuracy, can escape their scrutiny. This link is like laying a solid foundation for the entire production process, ensuring that every subsequent step can proceed smoothly with high-quality materials.
In the laser cutting workshop, two advanced laser cutting machines are like two highly skilled magicians, accurately cutting the hard steel into various shapes. The laser beam, with its extremely high energy and precise control, shuttles freely on the material, cutting edges that are smooth and flat with minimal dimensional errors. This not only improves production efficiency but also provides convenience for subsequent processing steps.
In the machining area, various equipment plays an industrial symphony. Cutting equipment further refines the materials to prepare for processing different parts. The bending machine, with its powerful pressure, bends the steel into various angles, shaping the skeleton structure of the crane. The radial drilling machine and bench drilling machine accurately drill the required holes in the material, providing connection points for subsequent assembly. The CNC lathe, with its high-precision machining ability, finely processes key components to ensure that their dimensions and surface quality are optimal. The grinding wheel machine is responsible for grinding the processed parts to remove burrs and uneven places, making the surface smoother. The milling machine and boring machine play an important role in the processing of complex parts. They can process grooves and holes of various shapes to meet the special requirements of the crane structure.
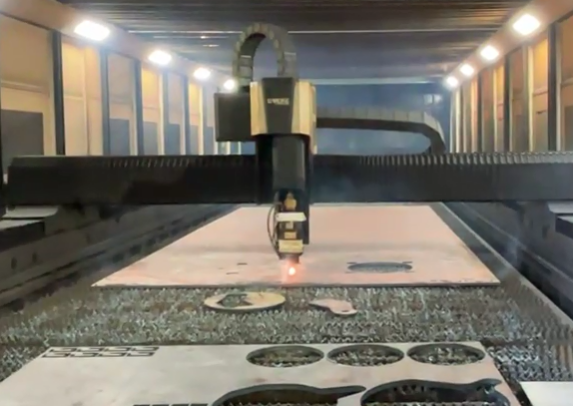
In the machining area, various equipment plays an industrial symphony. Cutting equipment further refines the materials to prepare for processing different parts. The bending machine, with its powerful pressure, bends the steel into various angles, shaping the skeleton structure of the crane. The radial drilling machine and bench drilling machine accurately drill the required holes in the material, providing connection points for subsequent assembly. The CNC lathe, with its high-precision machining ability, finely processes key components to ensure that their dimensions and surface quality are optimal. The grinding wheel machine is responsible for grinding the processed parts to remove burrs and uneven places, making the surface smoother. The milling machine and boring machine play an important role in the processing of complex parts. They can process grooves and holes of various shapes to meet the special requirements of the crane structure.
The welding workshop is a bustling scene. Welding processes such as leg welding, large frame welding, turntable welding, and boom welding are carried out in an intense and orderly manner. Welding technicians, holding welding guns like waving magic wands, firmly connect the components together. With their superb skills and rich experience, they ensure that every weld is strong and reliable and can withstand the huge pressure of the crane during operation. During the welding process, strict quality control measures ensure the stability and reliability of welding quality. From the control of welding current and voltage to the visual inspection of welds, every link is refined to perfection without the slightest error. At the same time, the welding process should comply with standards such as “Code for Welding of Steel Structures” (GB 50661). The weld appearance should be uniform and smooth without cracks, pores, slag inclusions, and other defects. The welding strength should meet the bearing requirements of the crane under various working conditions. For welding different materials of steel, appropriate welding processes and welding materials should be used to ensure the quality of welded joints.
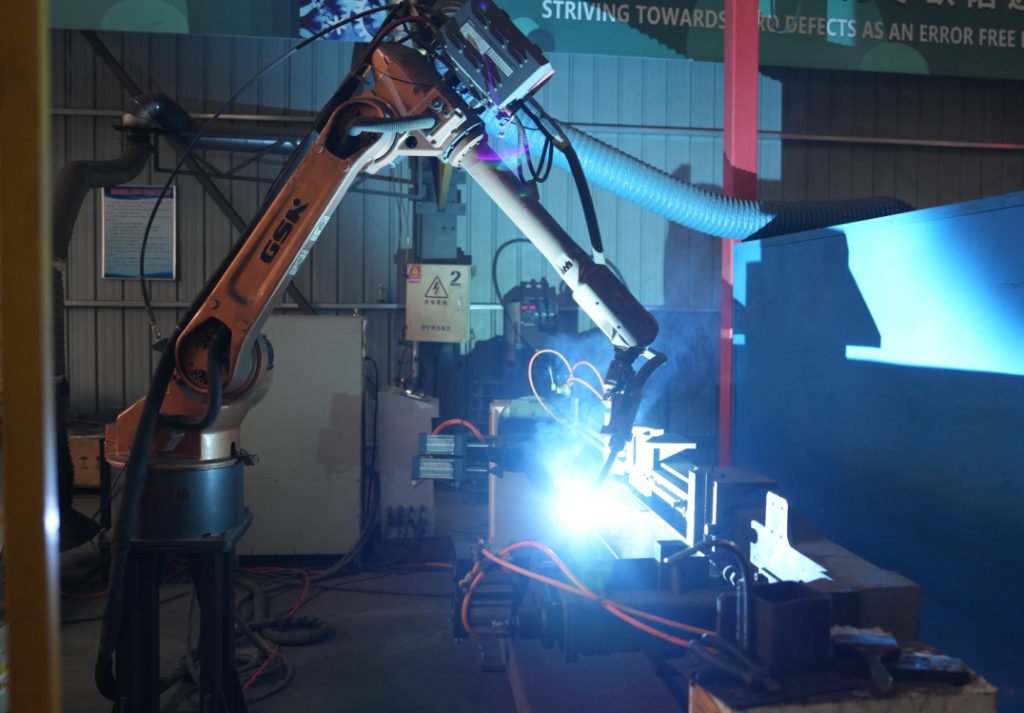
The shot blasting and powder coating process gives the crane a strong and beautiful coat. Surface treatment of the loading material is the first step in this process. By cleaning the impurities and oil stains on the material surface, it prepares for subsequent shot blasting and powder spraying. The loading hanger suspends the crane parts on the production line so that they can pass through each process smoothly. The shot blasting process uses high-speed sprayed steel shots to remove the oxide scale and rust on the material surface and increase the surface roughness of the material to improve the adhesion of powder spraying. The cleaning (phosphating) process further cleans the material surface and forms a phosphating film on its surface to enhance corrosion resistance. The preheating and drying process evaporates the moisture on the material surface to create good conditions for powder spraying. During the powder spraying process, the powder coating evenly adheres to the surface of the crane parts, forming a beautiful and durable coating. The secondary preheating and drying and the tertiary drying make the powder coating fully cured to ensure the quality and performance of the coating. Shot blasting treatment should comply with standards such as “Rust Grades and Preparation Grades of Steel Surfaces Before Painting” (GB/T 8923), and the powder coating quality should comply with standards such as “Technical Conditions for Powder Electrostatic Spraying Coatings” (GB/T 18593). The coating should be uniform and firm without blistering, peeling, cracks, and other defects. The coating thickness should meet the design requirements to ensure corrosion resistance.
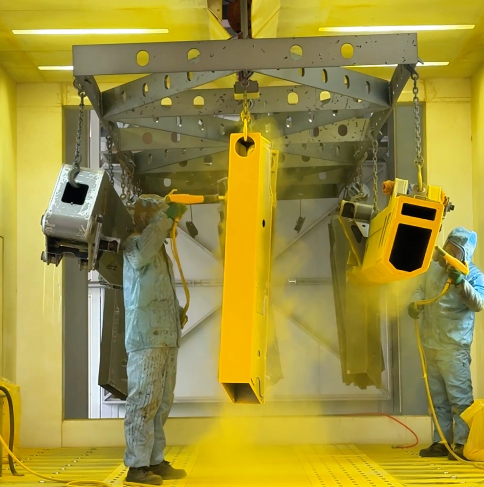
The installation stage is the key link in the formation of the crane. Chassis assembly (large frame) assembles the bottom structure of the crane, providing stable support for the entire crane. Upper assembly (turntable + upper mounting rod seat) installs the upper rotating structure and rod seat of the crane in place, providing flexibility for the crane’s operation. Assembling the large rod is an important step in the installation process. As the main working part of the crane, the installation accuracy of the large rod directly affects the performance and safety of the crane. Electrical installation provides power and control for the crane, enabling it to operate according to the predetermined program. During the installation process, strict quality control measures ensure the installation accuracy and connection reliability of each component. The tightening force of every screw and the connection of every wire are carefully debugged and inspected to ensure that the crane will not have any failures during operation. Assembly accuracy should comply with standards such as “Crane Design Code” (GB/T 3811). The assembly gaps, parallelism, and perpendicularity of each component should be controlled within the specified range to ensure the smooth operation and reliability of the crane. During the assembly process, the assembly process sequence should be strictly followed, and the assembly sequence should not be changed without authorization. At the same time, appropriate assembly tools and methods should be used to ensure assembly quality.
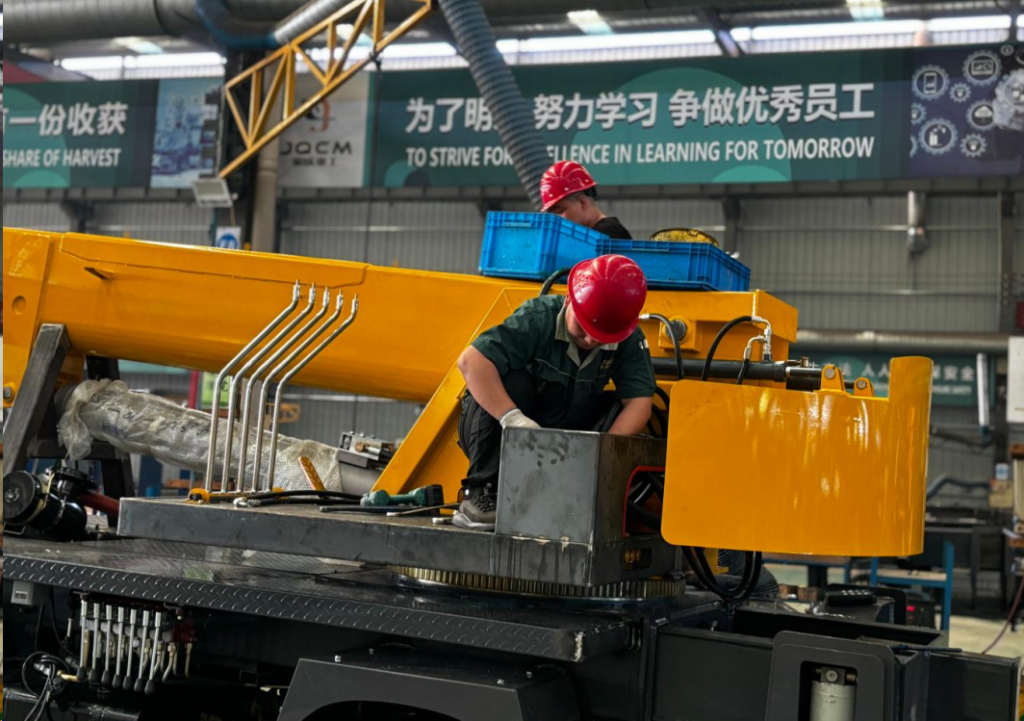
Finally, a series of strict inspection links such as performance testing, announcement size inspection, appearance inspection, final inspection, and PDI factory inspection provide a strong guarantee for the quality and safety of the crane. Performance testing includes tests on the lifting capacity, rotation speed, and walking stability of the crane to ensure that it can meet the requirements of various working conditions in actual operation. The announcement size inspection ensures that the size of the crane complies with the requirements of relevant national standards and regulations to avoid size discrepancies during use. The appearance inspection mainly checks the surface quality, coating integrity, and clarity of markings of the crane, making the crane not only have good performance but also a beautiful appearance. The final inspection and PDI factory inspection are comprehensive inspections and debugging of the crane to ensure that every crane leaving the factory is in the best condition.
The production equipment of the crane factory also needs to comply with a series of strict industry standards. Lifting equipment such as overhead cranes and gantry cranes should comply with standards such as “Safety Regulations for Lifting Machinery” (GB 6067). The rated lifting capacity, lifting height, span, and other parameters of the lifting equipment should meet production needs, and the safety devices of the equipment should be complete and reliable. The regular inspection and maintenance of lifting equipment should be carried out in accordance with relevant standards to ensure the safe operation of the equipment. Cutting equipment such as laser cutting machines and flame cutting machines should comply with standards such as “General Technical Conditions for Safety Protection of Metal Cutting Machines” (GB 15760). The cutting accuracy, cutting speed, and other performance parameters of the equipment should meet production requirements, and the safety protection devices of the equipment should be complete. Bending equipment such as bending machines should comply with standards such as “Safety Technical Requirements for Bending Machines” (GB 27607). The bending force, bending angle, and other parameters of the bending machine should meet production requirements, and the safety protection devices of the equipment should be complete. Drilling equipment such as radial drilling machines and bench drilling machines should comply with standards such as “General Technical Conditions for Safety Protection of Metal Cutting Machines” (GB 15760). The drilling accuracy, drilling speed, and other performance parameters of the drilling equipment should meet production requirements, and the safety protection devices of the equipment should be complete. The CNC lathe should comply with standards such as “Safety Requirements for CNC Lathes and Turning Centers” (GB 15760). The machining accuracy, machining efficiency, and other performance parameters of the CNC lathe should meet production requirements, and the safety protection devices of the equipment should be complete. Other equipment such as grinding wheel machines, milling machines, and boring machines should also comply with corresponding safety technical standards. The operators of these equipment should be professionally trained to be familiar with the operation methods and safety precautions of the equipment to ensure the safe operation and machining quality of the equipment.
With advanced production equipment, rigorous technological processes, and a professional technical team, this crane factory constantly pursues excellence and provides high-quality crane products for customers. In every link, it reflects the factory’s persistent pursuit of quality and high responsibility to customers. From the selection of raw materials to the factory inspection of the final product, every crane has gone through countless carefully crafted processes, condensing the wisdom and sweat of all employees.
In the future development, the crane factory will continue to adhere to the business philosophy of “quality first, customer first”, continuously introduce advanced technologies and equipment, improve production efficiency and product quality. At the same time, the factory will also strengthen cooperation and exchanges with domestic and foreign customers, continuously expand the market, and make greater contributions to promoting industrial development. It is believed that with the joint efforts of all employees, this crane factory will surely shine more brightly in the industrial field and become a leading enterprise in the industry.